Understanding Electric Molding: A Comprehensive Guide
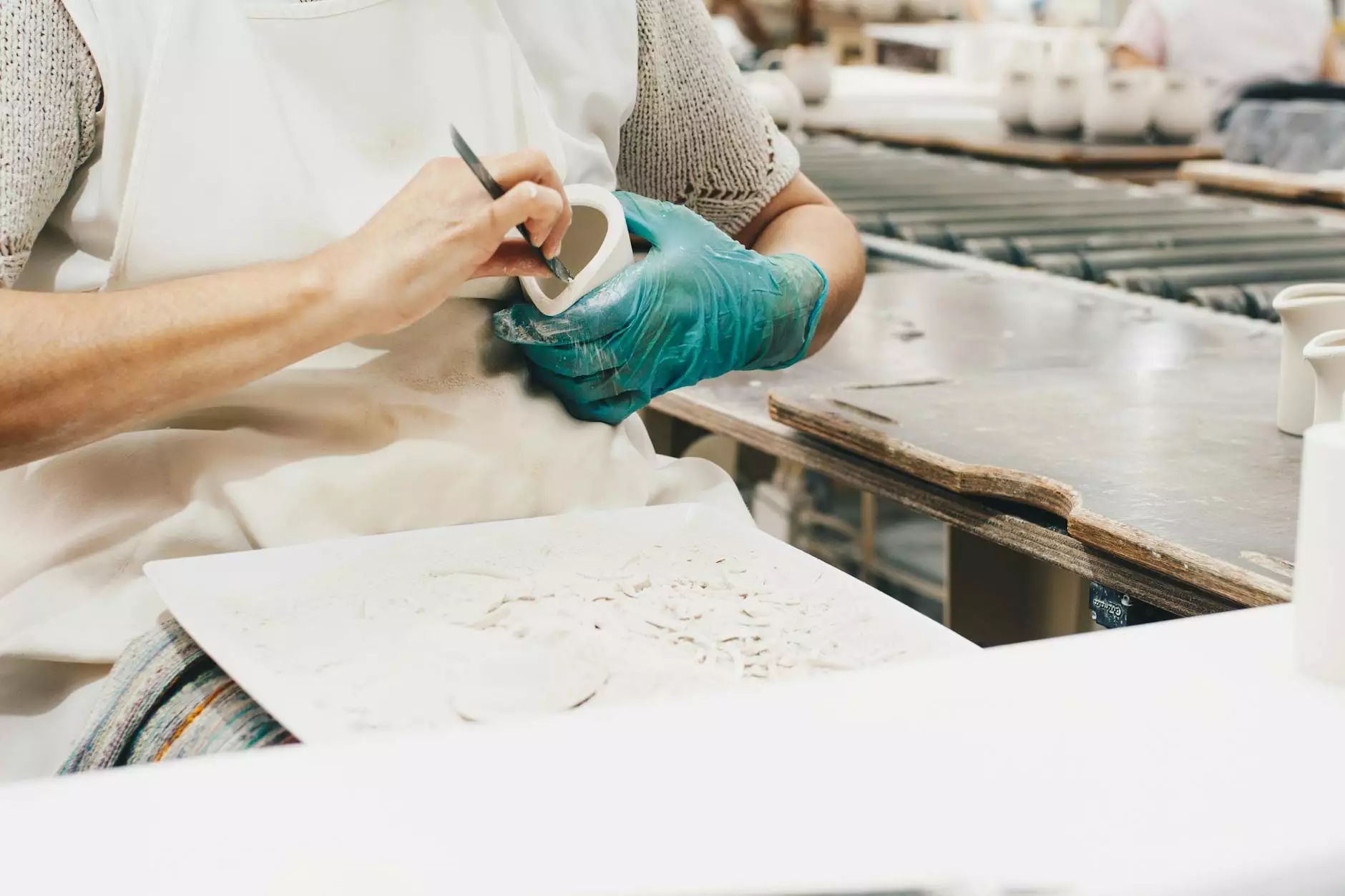
In today’s fast-paced manufacturing environment, electric molding has emerged as a leading process that combines technology and innovation to create high-quality products efficiently. This article delves into the nuances of electric molding, its applications, and the benefits it brings to metal fabricators and other industries. Here at DeepMould.net, we aim to provide valuable insights to help businesses thrive.
What is Electric Molding?
Electric molding refers to a manufacturing process where heat and pressure are applied to form materials—typically thermoplastics—into desired shapes. This process is powered by electric energy rather than conventional hydraulic systems, leading to increased precision and efficiency. Electric molding machines utilize electrical heaters and motors to control temperatures and forces applied during the molding process, resulting in enhanced control over the production.
How Electric Molding Works
The electric molding process can be broken down into several critical steps:
- Material Preparation: Raw material, usually in the form of pellets or granules, is fed into a hopper where it undergoes a heating process.
- Melting: The material is heated to a specific temperature using electrical resistance heaters to melt it into a viscous state.
- Molding: The molten material is injected into a mold cavity where it takes the desired shape.
- Cooling: The mold is cooled to solidify the material, ensuring that it retains the shape.
- Demolding: The finished product is removed from the mold, completing the process.
Benefits of Electric Molding
Electric molding offers numerous advantages that make it a preferred choice for manufacturers:
- Energy Efficiency: Electric molding machines consume less energy compared to their hydraulic counterparts, resulting in reduced operational costs.
- Precision and Control: The electric system allows for more precise control over temperature and pressure, leading to higher quality products.
- Consistent Quality: The consistent application of heat and pressure ensures uniformity in product quality, reducing defects.
- Lower Maintenance Costs: Electric machines have fewer moving parts, which translates into lower maintenance requirements and costs.
- Faster Cycle Times: With quick response times for heating and cooling, electric molding can reduce production cycle times, increasing overall productivity.
Applications of Electric Molding
The versatility of electric molding allows it to be utilized across various industries, showcasing its adaptability:
1. Automotive Industry
Electric molding is extensively used in the production of automotive components due to its ability to create precise and complex parts. From dashboard components to intricate engine parts, this process meets the demanding standards of the automotive sector.
2. Consumer Electronics
The consumer electronics industry benefits from electric molding through the manufacturing of casings, buttons, and intricate components that require high accuracy. These parts must not only fit perfectly but also endure everyday use.
3. Medical Devices
In the medical field, electric molding is used to produce devices and components that require strict compliance to safety and quality standards. Items such as syringe bodies, valves, and surgical tools benefit from precision that electric molding provides.
4. Home Appliances
Various home appliances are made using electric molding, where the process supports the production of high-quality and durable plastic components for items like refrigerators, washing machines, and microwaves.
The Future of Electric Molding
As technology continues to evolve, so does the electric molding process. Here are some trends shaping its future:
1. Integration of Smart Technology
With the rise of Industry 4.0, the integration of IoT (Internet of Things) in electric molding machines is on the horizon. This technology will allow for real-time monitoring and control of the production process, enhancing efficiency and reducing downtime.
2. Sustainability Practices
As industries shift towards sustainable practices, electric molding machines are being designed to further minimize waste and energy consumption, aligning with global efforts to reduce the carbon footprint of manufacturing.
3. Advanced Materials
The development of new materials, such as bio-based plastics and composites, opens new avenues for electric molding. These materials can enhance product performance while adhering to eco-friendly initiatives.
Challenges Facing Electric Molding
Despite its advantages, electric molding faces certain challenges:
- High Initial Investment: The cost of electric molding machines can be higher than traditional hydraulic machines, which may deter smaller manufacturers.
- Technological Expertise: Operating electric molding machines requires a skilled workforce familiar with the technology, which can be a barrier for some companies.
- Material Limitations: While effective for thermoplastics, electric molding may not be suitable for all types of materials, limiting its versatility.
Conclusion
The evolution of electric molding represents a significant milestone in manufacturing technology. Its energy efficiency, precision, and broad applicability make it an essential process for industries ranging from automotive to medical devices. While challenges exist, the future looks promising as advancements in technology pave the way for more efficient and sustainable production methods. Companies like DeepMould.net are at the forefront of this innovation, helping metal fabricators and other industries maximize the potential of electric molding. By embracing this technology, businesses can enhance their operational efficiency, produce high-quality products, and stay competitive in an ever-evolving market.