Understanding the Power of Plastic Mold Injection in the Modern Manufacturing Landscape
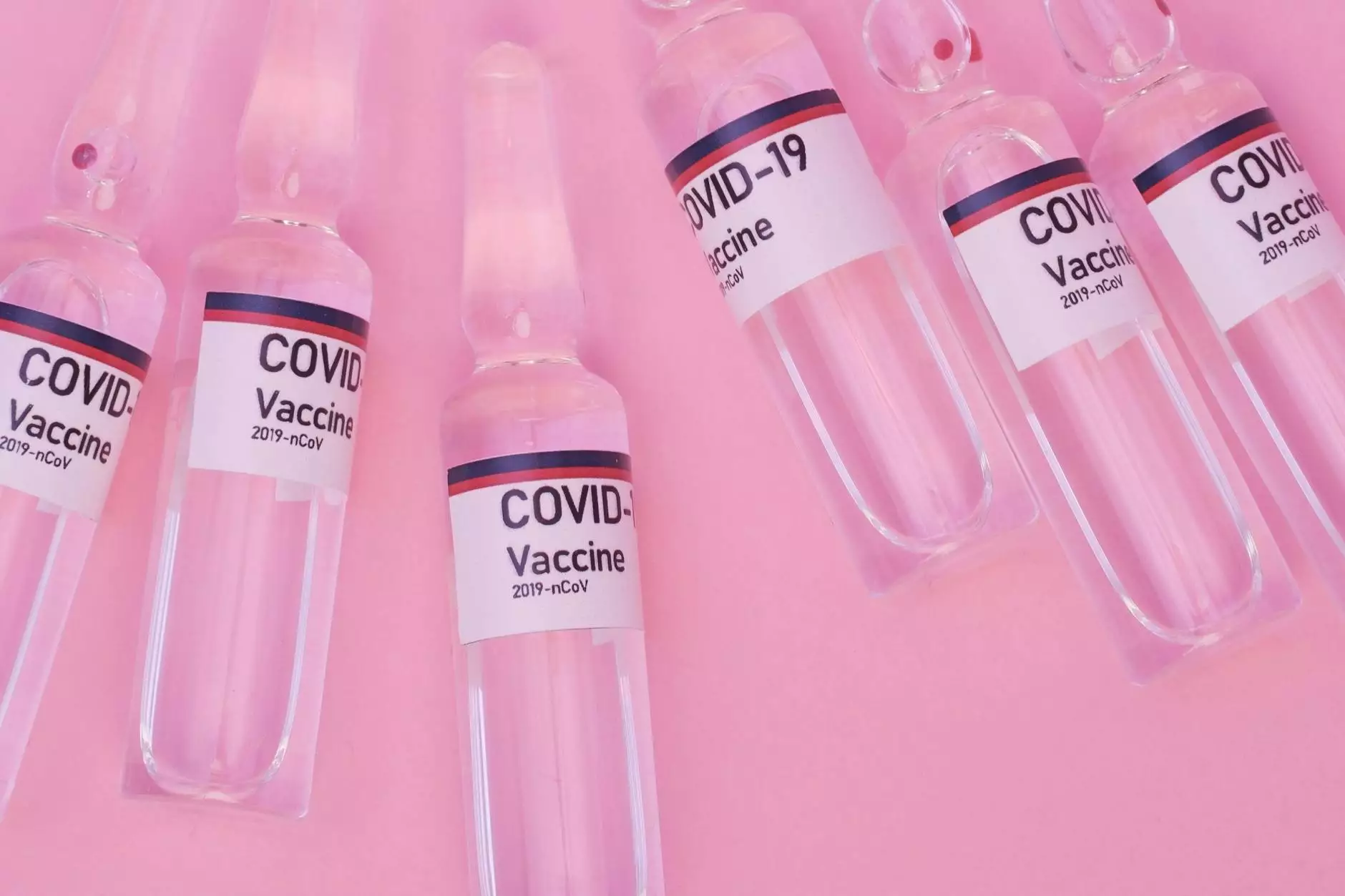
Plastic mold injection has emerged as one of the most significant advancements in manufacturing technology. This method allows for the production of intricate parts with precision and efficiency, revolutionizing the way products are designed and created. As industries continue to evolve, understanding the fundamentals and benefits of plastic mold injection becomes crucial for success.
What is Plastic Mold Injection?
At its core, plastic mold injection is a manufacturing process that involves injecting molten plastic into a mold to create a desired part or product. The process can be broken down into several key steps:
- Mold Design: The first step is designing a mold that allows for the desired shape and details of the final product. This involves computer-aided design (CAD) technology to ensure precision.
- Material Selection: Various plastics, such as thermoplastics or thermosetting plastics, can be utilized based on the requirements of the product.
- Heating and Injection: The selected plastic is heated to a molten state and then injected into the mold under high pressure.
- Cooling and Solidification: The molten plastic cools and solidifies to form the final product.
- Mold Removal: Once the product has cooled adequately, it is ejected from the mold, and any excess material is trimmed away.
The Advantages of Plastic Mold Injection
This manufacturing technique has numerous advantages, making it the preferred choice for many industries. Here are some of the standout benefits:
1. High Efficiency and Speed
Plastic mold injection is known for its rapid production capabilities. Once the initial mold is created, the process can produce parts in a matter of seconds, significantly reducing cycle times and increasing throughput.
2. Cost-Effectiveness
Although the initial investment in mold design and manufacturing may be high, the efficiency and scalability of plastic mold injection lead to lower costs per unit over time, making it a cost-effective solution for high-volume production.
3. Design Flexibility
This technique supports a wide range of complex designs and shapes that would be difficult, if not impossible, to achieve with other manufacturing methods. It allows manufacturers to innovate and create unique products.
4. Material Variety
Plastic mold injection accommodates various materials, including reinforced plastics, elastomers, and specialized compounds, enabling the production of diverse products to meet specific industry needs.
5. Enhanced Product Quality
The precision of the injection process ensures that each product meets stringent quality standards. Features such as consistent wall thickness and intricate details can be achieved reliably.
Applications of Plastic Mold Injection
The versatility of plastic mold injection means it finds applications across various industries, including:
- Automotive: Used to produce components such as dashboards, panels, and housing for electronic parts.
- Consumer Goods: Home appliances, toys, and kitchenware are commonly manufactured using this process.
- Medical Devices: Precision components for medical instruments and devices that require high reliability and sterility.
- Aerospace: Lightweight plastic components to enhance fuel efficiency and reduce overall weight without compromising safety.
- Electronics: Housings for smartphones, computers, and various electronic devices.
Challenges in Plastic Mold Injection
While plastic mold injection has numerous advantages, it is not without its challenges. Understanding these can help businesses strategize effectively:
1. Initial Setup Costs
The development of molds can be expensive and time-consuming, particularly for complex designs. This can be a barrier for small businesses or startups.
2. Material Limitations
Some materials may not be suitable for injection molding due to their properties, such as melting points or flow characteristics. Careful material selection is critical for success.
3. Design Constraints
While the design flexibility is one of its main advantages, there are still limitations regarding draft angles and the need for proper venting in the mold to ensure an efficient process.
Future Trends in Plastic Mold Injection
The landscape of plastic mold injection is continually evolving, driven by technological advancements and market demands. Here are some emerging trends to watch:
1. Sustainable Practices
With an increasing focus on sustainability, manufacturers are investing in biodegradable plastics and developing processes that minimize waste.
2. Smart Manufacturing
The integration of IoT (Internet of Things) technologies is allowing for smarter monitoring and optimization of injection molding processes, leading to improved efficiency and quality control.
3. Advanced Materials
Research into new materials is expanding the possibilities of what can be achieved with plastic mold injection. Innovations such as thermoplastic elastomers and composites are gaining traction.
Conclusion: Embracing the Future of Manufacturing
As the manufacturing sector continues to adapt and grow, plastic mold injection stands out as a crucial technology shaping the future. Its advantages in efficiency, cost-effectiveness, and design flexibility make it an attractive option for companies looking to innovate and thrive in a competitive landscape.
At DeepMould.net, we are committed to providing cutting-edge solutions in plastic mold injection. Our expertise in the field of metal fabricators ensures that you receive high-quality products and services tailored to your unique needs.
In summary, understanding the ins and outs of plastic mold injection is essential for any business aiming to succeed in today’s dynamic manufacturing environment. Embracing this technology can lead to significant advancements in product development and operational efficiency.